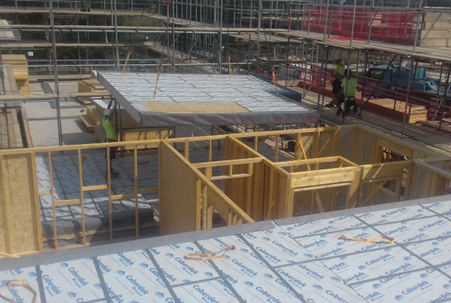
What Are The Stages of Timber Frame Building Installation?
1) Site And Build Preparation:
The first stage of timber frame building installation involves site preparation and creating the structural components themselves. Site preparation consists of clearing the area, setting the foundation stakes, and making sure the site is level. The construction team will also need to ensure that there is adequate access to the site, so they can transport materials and equipment easily. The timber frame itself is normally built off-site, and then transported to the site for assembly.
2) Loading And Unloading The Lorry:
The installation process starts with loading and unloading the lorry at site with the timber frame components! It's vital to load the last items of the lorry first and unload first items last to avoid damage to the components and to save your team set up time. The installation team typically consists of an appointed person (AP), a slinger/signaller, a crane driver, and two or more carpenters with specialist knowledge of timberframe installation.
3) Sole Plates:
Sole plates, also known as sill plates or bottom plates, are horizontal structural components that form the foundation of the timber frame structure, and the base for the wall framing system. Placement accuracy is therefore crucial. Sole plates are anchored to the foundation or floor slab and provide a key connection point for the vertical studs that make up the walls. Their primary function in timber frame construction is to distribute the weight of the structure evenly across the foundation, provide stability, and prevent moisture from seeping into the walls, while also maintaining the alignment and rigidity of the timber frame. The groundworkers and carpenters work closely together to ensure that the sole plates are level and securely fixed to the foundations.
4) Internal And External Walls:
The construction of internal and external walls is the next critical step in timber frame building installation. There are several types of walls you can use, including closed panel, open panel, and SIPs. Whichever type you choose, it’s essential that the walls have sheathing, insulation, and effective VR membranes. The sheathing acts as a protective layer for the building's exterior walls and can be made from a variety of materials, including plywood or oriented strand board (OSB). Insulation is installed at this stage to keep the building warm and energy-efficient by reducing heat loss, while VR membranes ensure the finished building has adequate ventilation.
5) Floors/Decks/Roofs
Ideally floors and/or decks are built on the ground or floor level and lifted into place by crane.
Roofs can be installed as individual pre-built trusses and structural roof beams, or as complete room-in-the-roof ‘top hats’, which are built on site and then lift into place.
The floors of timber frame buildings are load bearing structures, so must be strong enough to support the walls and roof. You must also make sure that these elements have enough insulation and are adequately sealed to exclude moisture.
These stages are critical for ensuring that the building's structural integrity is maintained. Safety and quality considerations are essential as any mistakes can cause damage to structures or workers.
6) Cladding And Roofing
Cladding and roofing materials complete the structural elements of the build and make the building weathertight. Cladding is the outer layer that covers the building's walls and exterior, improving thermal efficiency, while the roofing is designed to protect the structure from the elements. Cladding and roofing can be made from a range of materials, including brick, stone, metal, tiles, or slate – not just wood.
7) Finishing Touches:
The finishing touches of a timber frame project involve the installation of fascias, soffits, chimneys, DPC and VCL battens, and party wall U-value packs. Fascias and soffits are installed to protect the building's exterior walls from the wind and rain, while chimneys are essential for ventilation – even if the property does not have a solid-fuel-burning stove. DPC and VCL battens are installed to prevent moisture from entering the building, while party wall U-value packs are installed to meet the required energy efficiency standards and environmental regulations for new builds.
8) Essential Considerations:
Several essential elements must be considered during the timber frame building installation process. These include good design practices, communication between onsite and offsite stakeholders, safety, accuracy of installation, understanding the threat of disproportionate collapse (structural failure or damage that occurs when small or localised faults in the timber framework lead to a disproportionate loss of structural integrity), excellent fire safety during construction, accurate fireproofing of the building, technical knowledge and expertise of the installation team, and air tightness.
Find Out More
SC4 Carpenters are specialist timber frame installers based in Hampshire, with an area of operation that covers the south of England. If you’d like to discuss your project outcomes with one of our team, or find out more about timber frame construction, please get in touch today.
Click on the categories below to find out more about:
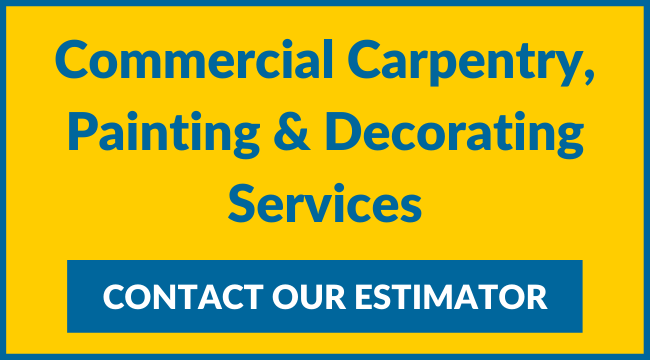
Connect with Us
Share this Page
More Posts
Recent Posts
- Case Study: Timber Frame Installation in Netley Grange, Southampton
- Commercial Decorating Services For Your Project’s Finishing Touch
- Choose An STA-Accredited Installer For Timberframe Installation
- Commercial Carpenters In Andover: How SC4 Can Help You Complete Your Project On Time
- Why The Right Second-Fix Construction Company Will Save You Time
- Targeted Support Crucial for Neurodivergent Workforce in Construction, Data Reveals